Electromagnetics and its impact
The theory of electromagnetism has an astonishing range of applications today. If Faraday and Maxwell could see how many devices rely on their discoveries, they would be astounded. Given the profound impact of these discoveries, many scientists consider these two pioneers among the most influential figures since 1600. In this brief note, I will explain how metal detectors operate using electromagnetic principles. Moreover, we will explore how electromagnetic software like EMS is pivotal for companies that design and manufacture metal detectors, enhancing functionality and design precision.
Concept of modern metal detectors
The operation of a metal detector is simple yet effective. It detects metals in places like beneath soil or inside rocks and is invaluable for finding everything from landmines to gold.
Metal detectors typically feature two coils: a transmitter and a receiver. The transmitter coil carries an alternating current at high frequencies (1-10 kHz), creating a magnetic field. This field induces a calibrated Eddy current in the receiver coil. When near metallic or ferromagnetic materials, the metal also generates an opposing magnetic field due to an induced Eddy current. This interaction reduces the Eddy current in the receiver coil, which a sensor detects as a drop from the expected level, signaling the presence of metal. In the diagram, the orange coil is the transmitter, and the green coil is the receiver, set to detect changes in current flow.
Figure 1 - Simple arrangement of coils in a metal detector
Role of EMS in designing a metal detector
For engineers tasked with developing a metal detector, several critical design factors must be assessed to turn the concept into a functional product. Tools like CAD and EMS Simulation software are indispensable for addressing these considerations. The key questions to explore include:
- What is the optimal size for the coil?
- What frequency and magnitude of AC current should be applied?
- What is the induced current in the receiver coil when there is no metal nearby?
- How can the entire setup be packaged effectively into a product?
Using CAD and EMS software, designers can answer these questions comprehensively. Once a preliminary coil design is established, EMS allows for virtual testing to visualize crucial engineering parameters, such as the magnetic flux density in the coils, ensuring all design specifications are optimized before moving to physical prototypes.
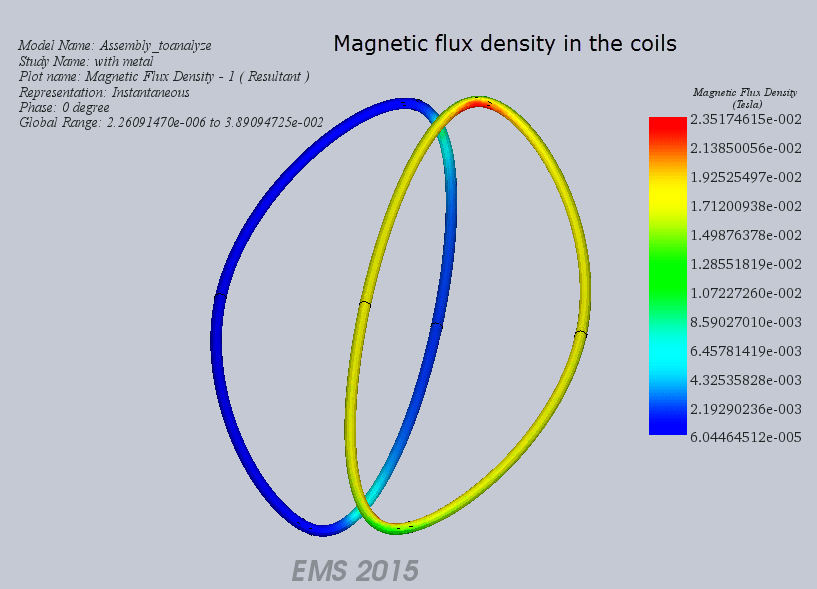
Figure 2 - EMS can plot the magnetic flux density in the coils
EMS product will also give you the value of the induced current in the receiver coil.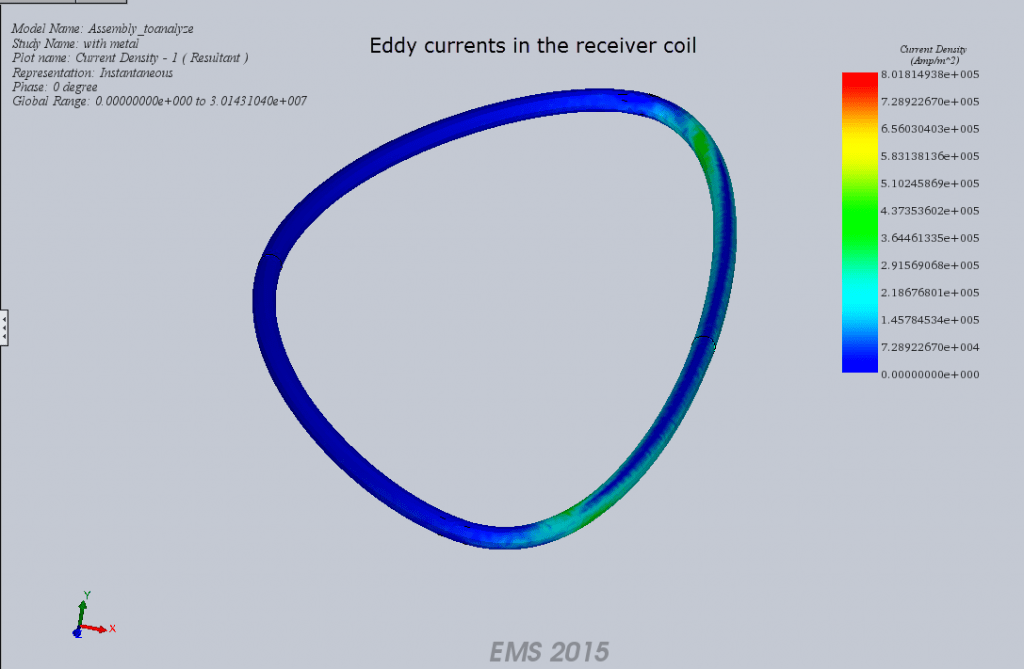
Figure 3 - Plot of the eddy current density in the receiver coil
Crucially, CAD and EMS Simulation software allow engineers to model a variety of hypothetical scenarios to refine the design of metal detectors. For example, engineers can simulate changes in the induced current in the receiver coil when a metallic object is detected at a specific distance. Additionally, EMS provides the ability to compare the induced eddy currents in the receiver coil, both with and without the presence of a metallic object. This advanced modeling capability ensures that the product can be meticulously perfected, optimizing design parameters and resolving potential issues before a physical prototype is even created and tested.
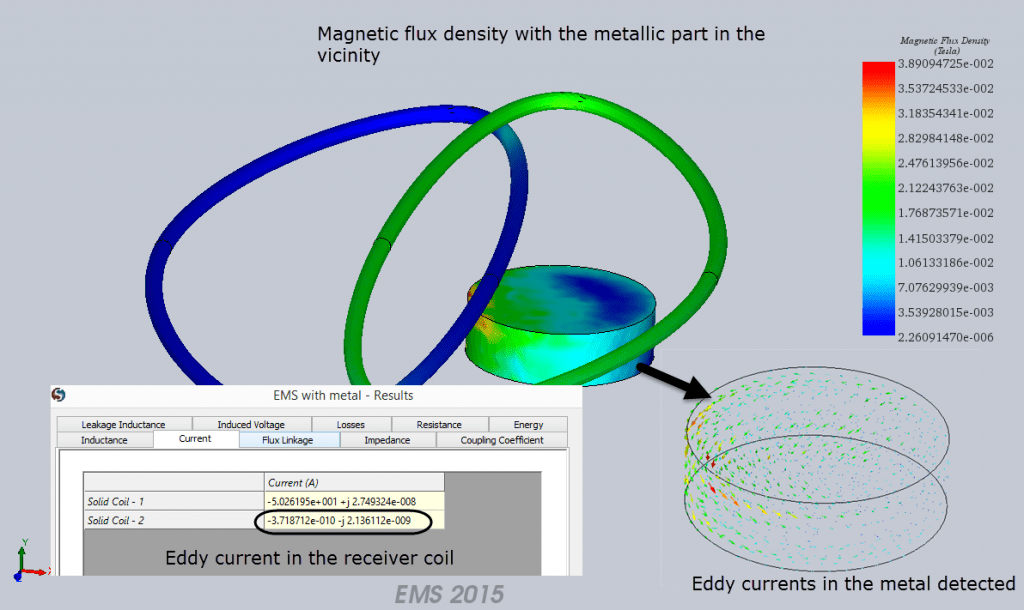
Figure 4 - EMS plots with the presence of a metallic part
Figure 5 - Compare the eddy currents induced in the presence of a metallic part with the ideal case
Advantages of this approach
The benefits of using simulation in product development are well-documented, with many engineers achieving significant improvements through this approach. First and foremost, simulation greatly accelerates the process of bringing a concept to market. By reducing the need for multiple prototypes, it also lowers the overall cost of product development. Many companies that employ simulation find that their first prototype, with only minor adjustments, often becomes the final product. Additionally, simulation fosters innovation in product development by allowing engineers to explore numerous "what-if" scenarios. This enables thorough testing and optimization of various designs, ensuring that the best possible solution is identified and implemented.
Conclusion
The integration of EMS electromagnetic simulation into metal detector design not only streamlines the development process but also enhances product precision and efficiency. By allowing engineers to simulate and refine various scenarios before physical prototyping, EMS ensures that each design phase is optimized for performance. This capability not only saves time and resources but also fosters innovation by making it feasible to test multiple "what-if" scenarios quickly. As a result, companies can bring more effective and reliable products to market faster than ever, demonstrating the powerful impact of simulation technology in modern engineering.